Bioenergy Devco proposes poultry waste recycling plant
The poultry industry is the economic driver fueling the agriculture industry.
In 2020, Delmarva poultry farmers raised 570 million birds, and poultry plants processed 4.2 billion pounds of poultry at a value of $3.4 billion.
Handling waste from the industry has been an ongoing issue as government officials and farmers search for effective ways to dispose of waste and protect the environment.
Most waste – manure or litter from poultry houses and DAF from processing plants – is used as fertilizer on farm fields or is applied to land using spray-irrigation systems.
DAF, or dissolved air flotation, is the liquified end product of wastewater treatment at poultry processing plants.
Now, there is a major push across the region to develop poultry waste recycling plants. And who knew part of the solution would be microorganisms?
It's the microorganisms that break down the waste.
One of the international leaders in that push, Bioenergy Devco, based in Annapolis, Md., has plans to build a $35 million-$40 million recycling plant at the site of its composting facility south of Seaford along Route 13A.
Currently, the plant – purchased by the company a year ago from Perdue Farms – produces compost from poultry processing plant waste.
Under the new plan, the waste, primarily from Perdue plants, would be recycled into compost and natural gas.
The company is building a similar plant in Jessup, Md., which will process food waste.
The company has filed a conditional-use application to amend four other conditional-use permits issued over the past three decades for the project to convert poultry processing plant waste into natural gas and compost using an anaerobic digester process.
“We've been here for 30 years and we want to be an important part of the community,” said Peter Ettinger, Bioenergy Devco's chief development officer. “We need to find an environmentally savvy way to manage these materials.”
After the first public hearing on Feb. 11 before Sussex County Planning and Zoning Commission, members deferred a vote for further consideration.
Sussex County Council will hold a public hearing on the application at 10 a.m., Tuesday, March 16, in the Carter Partnership Center at Delaware Technical Community College in Georgetown.
The composting process
In the current composting operation, poultry processing waste is mixed with wood chips in a large mixing facility. From there, the material is piled into large bunkers where it is covered and its temperature monitored.
Plant manager Jeff Deats said maintaining a temperature around 160 degrees is critical to the process, which also includes constant aeration. He said it's the oxygen and heat that combine to break down the material into usable compost.
After about 30 days in the bunker pile, the material is moved to another area where it is rotated and mixed for another 30 days.
The final stage is a screening operation where any piece of wood larger than three-eighths of an inch is removed. Deats said those wood chips are then reused in the mixing process.
The finished compost, which has broken down to a fine soil-like material, is moved again to large piles where it is subject to DNREC-required testing for nutrient content.
In all, Deats said, it can take as long as four to five months before the compost is ready to be sold.
“There is a demand for our material, there is no doubt about it,” Deats said.
The compost is sold to companies that blend it with other soil amendments, bag it and sell it commercially.
Anaerobic digesters key to process
The biggest change in the current operation would be the addition of four anaerobic digesters to the process.
The anaerobic process begins with the processing plant waste delivered via truck to a receiving building, which is enclosed under negative pressure to capture odors. The air from the receiving building is captured and filtered.
The waste is pumped into holding tanks and then one of four digesters. The material is heated and constantly mixed for about 30 days. Microorganisms break down the material, which is called digestate.
The liquid can be used as a soil amendment to improve soils on farmland. But because of the facility's existing market for compost, a centrifuge would be used to remove excess water from the digestate, with the remaining solid material transferred to the composting facility. There it would be processed with wood waste to make organic compost.
The microorganisms release biogas, which is a mixture of methane, carbon dioxide, water vapor, and traces of hydrogen sulfide and ammonia. The gas will be captured and scrubbed as part of the facility's process.
Chesapeake Utilities will take the biogas off site, clean it to renewable natural gas and inject it into the company's natural gas pipeline.
While the proposed plant would not process poultry house litter, another plant in Sussex County has been approved to recycle that waste.
CleanBay Renewables will build a $60 million plant to recycle up to 90,000 tons of litter from poultry houses at a site located off Route 113 south of Georgetown. The plant will convert the waste to electricity and fertilizer.
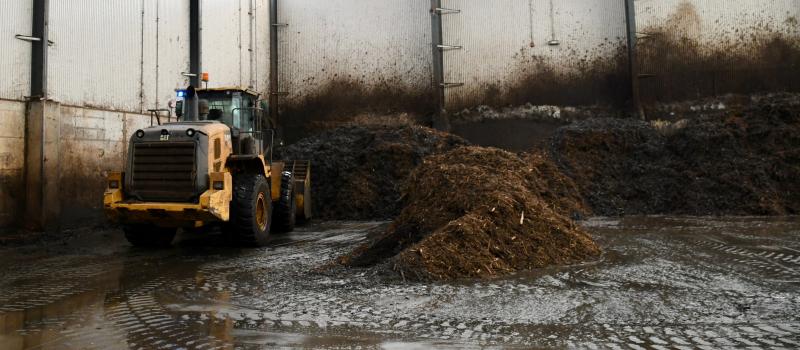

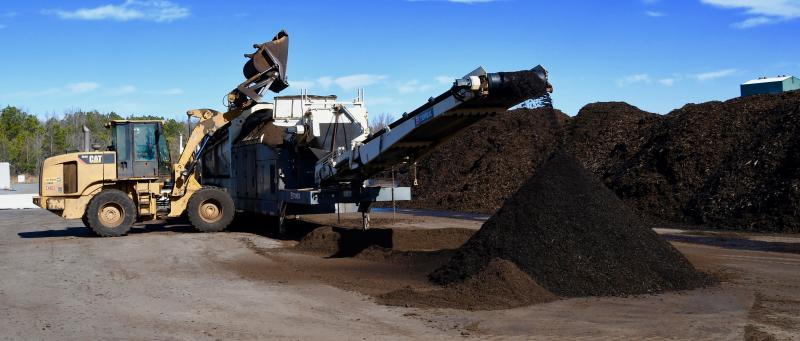
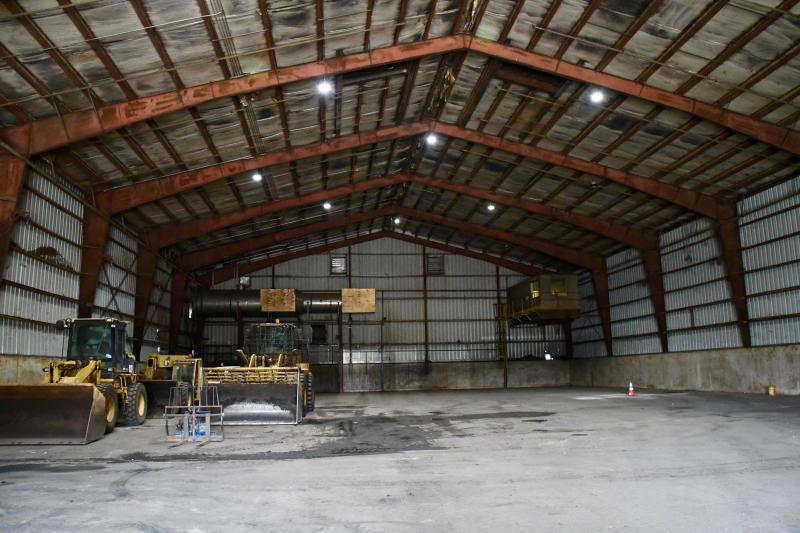
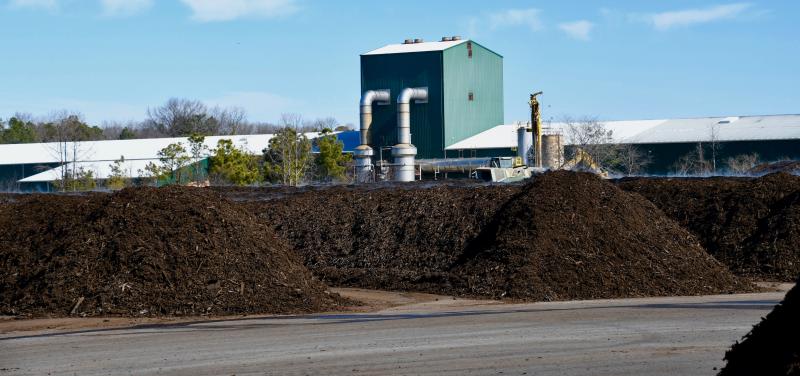
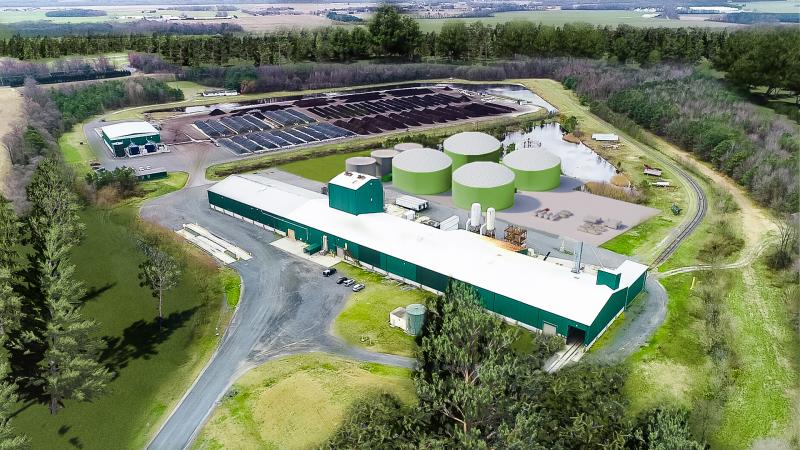
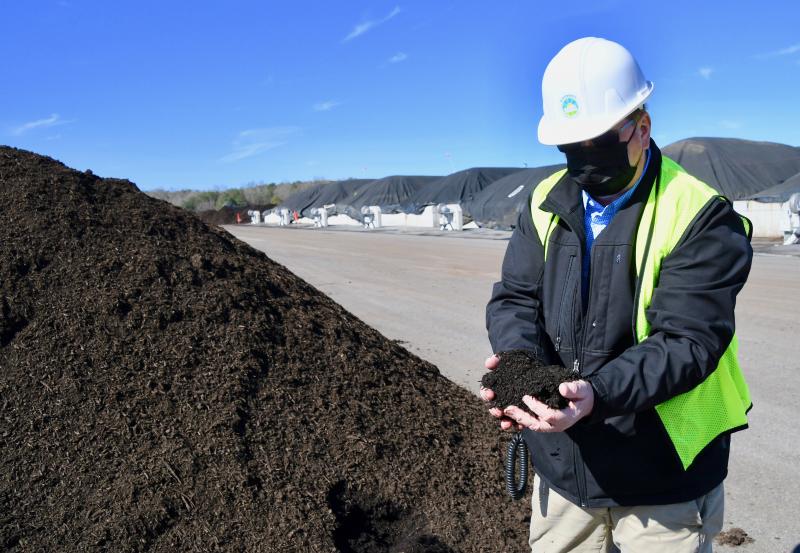